Promoting the rights and well-being of supply chain workers worldwide, the Ethical Supply Chain Program works with organisations to create a more transparent supplier network. Carmel Giblin, CEO and President, enlightens us on the importance of social compliance and fair labour standards.
TRANSFORMATION THROUGH TRANSPARENCY
In recent years, organisations across the world have endeavoured to promote a more transparent supply chain in order to increase customer, stakeholder, and employee satisfaction.
Regarding the latter, issues around social compliance and labour standards have increasingly become a major challenge in modern international supply chains, whilst it is widely recognised that more can be done to achieve sufficient workers’ rights and community empowerment.
To combat this challenge, major network players, including manufacturers, brands, licensors, and retailers, must establish a culture of collaboration and accountability.
“Crucially, it’s important that manufacturers feel they are in a supportive environment where they can disclose any issues. It is only when this happens that problems can be addressed and rectified,” opens Carmel Giblin, CEO and President of the Ethical Supply Chain Program (ESCP), a global non-profit organisation that exists to create a better life for supply chain workers worldwide.
Conversely, it is also important for organisations to provide clear guidance and communication on what they require from suppliers and other business partners.
“Issuing a supplier code of conduct is a good place to start, as it raises the question of whether suppliers can meet the expectations outlined and how they plan to do so,” informs Giblin.
“The focus should be on organisations working with suppliers to build a multi-year plan that outlines clear steps and the resources and processes needed at each stage to reach the end goal,” she adds.
For this reason, ESCP has become more important than ever, helping to steer supply chain entities towards greater consideration for social responsibility and compliance.
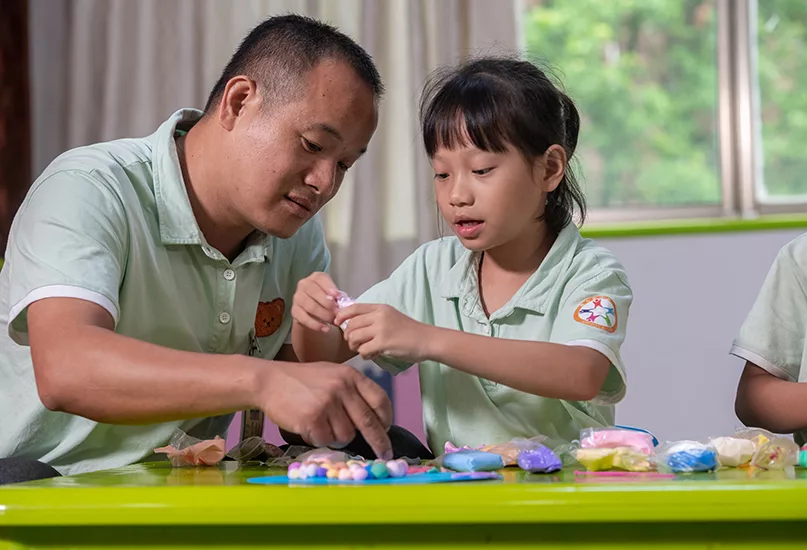
VALUABLE SUPPLIER SUPPORT
ESCP operates across a range of industries to partner with companies who are committed to ensuring that supply chain workers are treated with respect in a safe environment.
The organisation first began its journey in 2004 when the International Council of Toy Industries (ICTI) sought assurance that its members were complying with the high standards it had created to ensure workers in the industry were being treated fairly.
Today, ESCP has expanded far beyond the toy industry to partner with a vast range of sectors and deliver programmes that protect workers’ rights, the communities in which they operate, and the environments in which they live and work.
The organisation verifies the maturity of a business’s social compliance system by introducing key initiatives such as its Supplier Certification Programme and Social Impact Assessment, as well as the Worker Helpline, offering free, confidential information and advice for those in a range of sectors including manufacturing and construction.
“Our helpline has proven a highly effective grievance mechanism and an essential component for improving transparency and understanding the real issues on the ground in supply chains,” Giblin shares.
ESCP’s valuable support contributes to achieving true transparency across modern supply chains, which can prove difficult given the scale and complexity of global operations.
“Logistics is a prime example where several contractors are often required to fulfil customer expectations. Each of these subcontractors will engage its workforce in a different way, through flexible, temporary, and zero-hour models,” Giblin explains.
“You can quickly see how getting visibility across this workforce and the entire network isn’t straightforward.”
For example, companies utilising subcontractors will have less visibility and control over the conditions and contracts of the workers involved.
In fact, ESCP has witnessed many issues related to the non-payment of workers, serious breaches of health and safety standards, and even forced and child labour.
“Our data shows that breaches of labour standards are typically found to be more egregious further down the supply chain. That is why it is vital that companies seek to have a greater understanding of their supplier network,” urges Giblin.
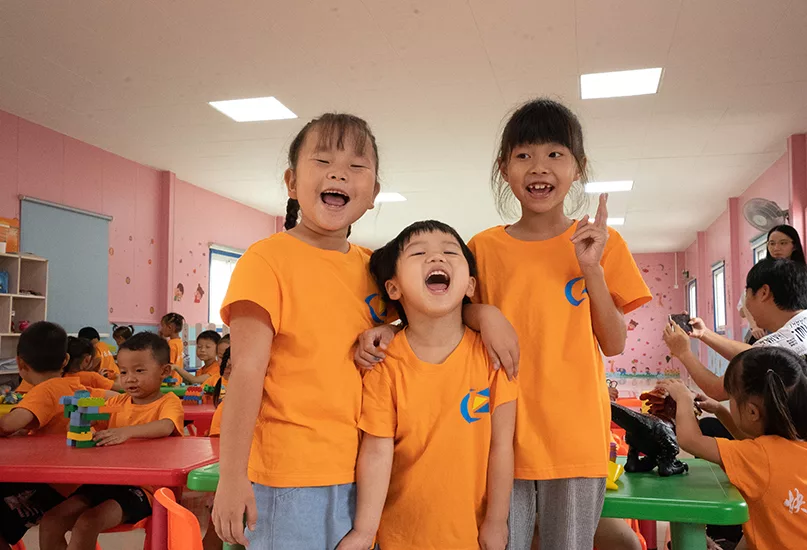
IMPLEMENTING CHANGE
ESCP delivers its support through a variety of comprehensive programmes and initiatives. The Supplier Certification Programme, for example, is designed to help suppliers meet their obligations for labour standards.
“One of the ways this is achieved is through factory audits that ensure facilities are operating ethically across areas such as employment practices, working hours, forced labour, and environmental, health, and safety standards,” Giblin outlines.
These audits ensure adherence to ESCP’s Code of Business Conduct, helping organisations implement effective control measures across their supply chains.
Additionally, the company is partnering with UNICEF to create the Family-Friendly Factory Programme, which has installed childcare and training facilities in factories worldwide.
“We began to develop the programme in 2015, triggered by wanting to do more with insights collected from workers during audit interviews and calls made to the Worker Helpline,” she recalls.
The helpline and interviews revealed that the leading reason workers were leaving their factory jobs was due to childcare issues. The results indicated that this was especially prominent in China, with the government estimating that more than 66 million children were uncared for in 2023 due to parents migrating for work.
“We wanted to provide a solution to help factory employees obtain safe and accessible childcare, all while solving labour shortage issues in the manufacturing industry.”
Therefore, by utilising UNICEF’s policy guidance and expertise and working with a subsidiary of Save the Children, ESCP developed a pilot programme known as Family-Friendly Spaces. This initiative witnessed the installation of childcare facilities and the training of teachers to run them at four piloting factories.
Funded by its suppliers and customers, the initiative has since achieved significant success and is on track to benefit 30,000 children throughout 100 childcare spaces in 50 factories by 2025.
The Family-Friendly Factory Programme is now being implemented beyond China into Vietnam and Mexico, with further geographical expansion plans in the pipeline.
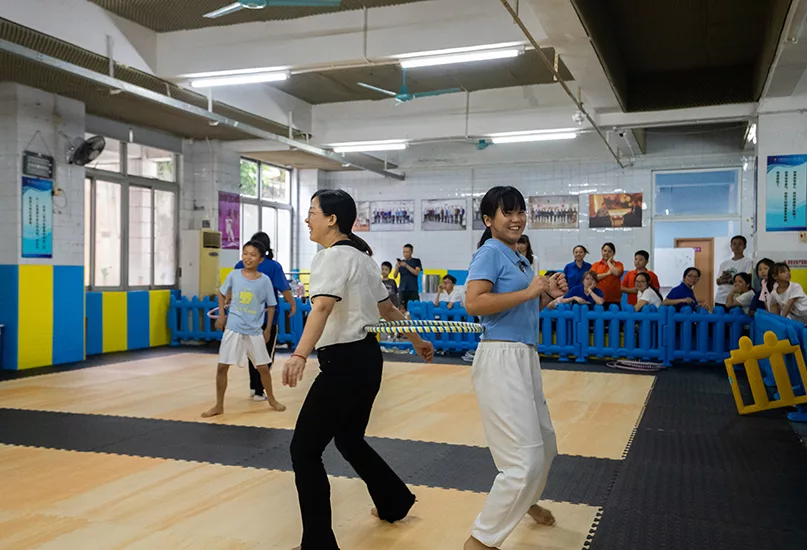
MOVING THE NETWORK FORWARD
Taking into consideration the supply chain horizon, scrutiny of the global network will continue to increase as more international legislation is introduced. As such, businesses across the world must adapt their processes to ensure transparency at every stage.
Going forward, it will not only become common practice to know the provenance of products in the supply chain but also the wages and hours worked of those who made them.
Therefore, programmes exist to enable companies to achieve the transparency needed and help their suppliers improve in an efficient and cost-effective way.
“Customers trust the brands they buy from, and if that trust is misplaced, customer confidence will be damaged and business lost. Knowing who is in your supply chain and ensuring they operate to the required standards is a company imperative,” Giblin closes.