Kapila Mehta, Sustainability Vice President of Power Products at Schneider Electric, outlines the implications of adapting global products and services to local markets.
Globalisation has enabled many multinational corporations to expand into new markets and achieve rapid growth, but being part of a larger network also makes them more vulnerable to external risks. Extreme weather or geopolitical conflict can cause unexpected disruptions, and globalised businesses can find their entire supply chain impacted by something out of their control.
Companies are increasingly building more regional approaches into their strategies to mitigate the effects of disruption. As a result, supply chains are undergoing a transformation known as ‘glocalisation’, which embraces both a global and local model.
As this transition takes place, many organisations are discovering that by going ‘glocal’, they can, in turn, improve their sustainability efforts and transparency. For these organisations, a hybrid strategy combining global and local can help promote resilience and sustainability.
WHAT DOES GLOCALISATION LOOK LIKE?
Transitioning from a global to a glocal supply chain model can significantly contribute to sustainability and resiliency. During the COVID-19 pandemic, for example, businesses were forced to adapt quickly, find creative ways to build resilience into their supply chains, and take advantage of resources a little closer to home. This shift, commonly known as glocalisation, empowers companies to adapt their supply chains to suit the specific needs of local markets.
By tailoring products and services to meet regional demands, businesses can establish a deeper connection with customers and communities while minimising the environmental footprint associated with long-distance shipping. Although metrics suggest we have made it through the worst stages of the supply chain crises, the trend towards glocalisation and local supply chains will likely continue. Glocalisation will prove vital as companies seek to improve their agility, competitiveness, customer experience, and global positioning.
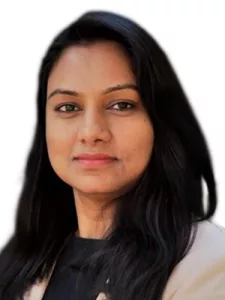
THE UNTAPPED POTENTIAL OF GOING GLOCAL
Embracing glocalisation and local supply chains offers numerous advantages for businesses. In an increasingly uncertain and dynamic global marketplace, companies can gain greater agility and flexibility through glocalisation, responding swiftly to individual market changes such as currency inflation and evolving customer preferences. A hybrid global and local approach enables companies to safeguard against unpredictable shocks in the future.
With this hybrid approach, striking the right balance is key. Global supply chains are favourable as they provide economies of scale; on the other hand, local supply chains bring more resiliency. With a balance between the two, companies can remain competitive whilst becoming more resilient and adaptable to changing market conditions and ensuring a consistent flow of goods and services during challenging times like natural disasters, geopolitical tensions, or product shortages. Multi-sourcing and onshoring play into this, with more local options being added to supply chain strategies to boost resilience.
Through glocalisation, businesses can empower the local communities in which they reside. By fostering strong ties with local suppliers and manufacturers, companies can contribute to developing regional economies, generating more employment opportunities, and nurturing a sense of community engagement.
AIMING FOR SUPPLY CHAIN GLOCALISATION
The benefits of glocalisation are clear, but what does this look like in practice? Building a network of factory and distribution centres in different regions can help maximise flexibility. Still, businesses need to establish what outcomes they want to achieve and understand the tools and resources they need to accomplish this.
At Schneider Electric, global and local supply chains have helped foster resiliency and self-sufficiency in each region where the company operates. Our smart factory in Lexington, Kentucky utilises smart manufacturing solutions to reduce energy costs and usage while improving operational efficiency. As a result, it has driven a 26 percent energy reduction, a 78 percent CO2 reduction in conjunction with renewable energy credits (RECs), and a 20 percent water use reduction – all whilst reducing equipment downtime by 20 percent. This is just one of nearly 300 factories and logistics centres across 40 countries which use Industrial Internet of Things (IIoT) solutions to create a customised, sustainable, and end-to-end connected supply chain.
During the pandemic and subsequent global shortages of parts such as semiconductors, it was vital to provide an agile response. Giving procurement teams the freedom to do whatever they needed to adapt quickly to changes in the market and continue meeting customers’ needs made supply chains more shock-resistant and customer-centred.
Nurturing relationships with partners and suppliers is crucial to building resiliency and ensuring operational continuity. Moreover, the growing emphasis on Scope 3 will require larger organisations to create transparency across their supplier network.
While glocalisation may be an essential part of this process, it also presents significant challenges. Key suppliers in specific parts of the world have the resources and structures to track emissions data and decarbonise operations. However, Tier 2 and Tier 3 suppliers operating in regions with insufficient regulatory support aren’t prepared or able to report their emissions. Businesses should still strive to reduce emissions however they can, but strengthening regulations around Scope 3 will significantly help accelerate decarbonisation.
As more organisations embark on the path of glocalisation, we can expect sustainability and resiliency to become a bigger priority. By adopting a hybrid approach that integrates global and local, businesses can improve their bottom line while positively impacting the environment and communities worldwide.